Part of the major upgrade is to increase the battery capacity 50% from 20Ah to 30Ah. This is being done to increase run time and also reduce volt droop at high current draw. The increase in capacity and size means the battery will no longer fit in the boot of the car so it will be relocated to the passenger seat well. This will also move the battery mass lower in the car and closer to the center of mass.
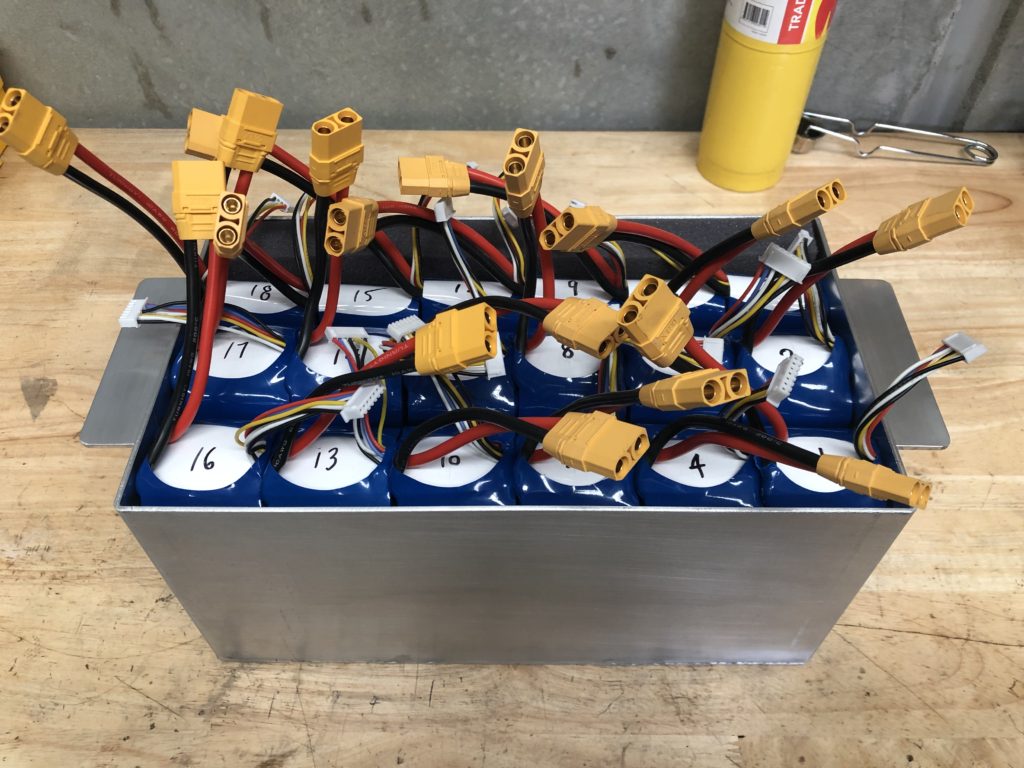
As the battery parallel string count has increased it has become difficult to manage all the electrical connections so a busbar arrangement for the main DC bus has been implemented. Cable size from each battery spring to the bus is 10mm2.
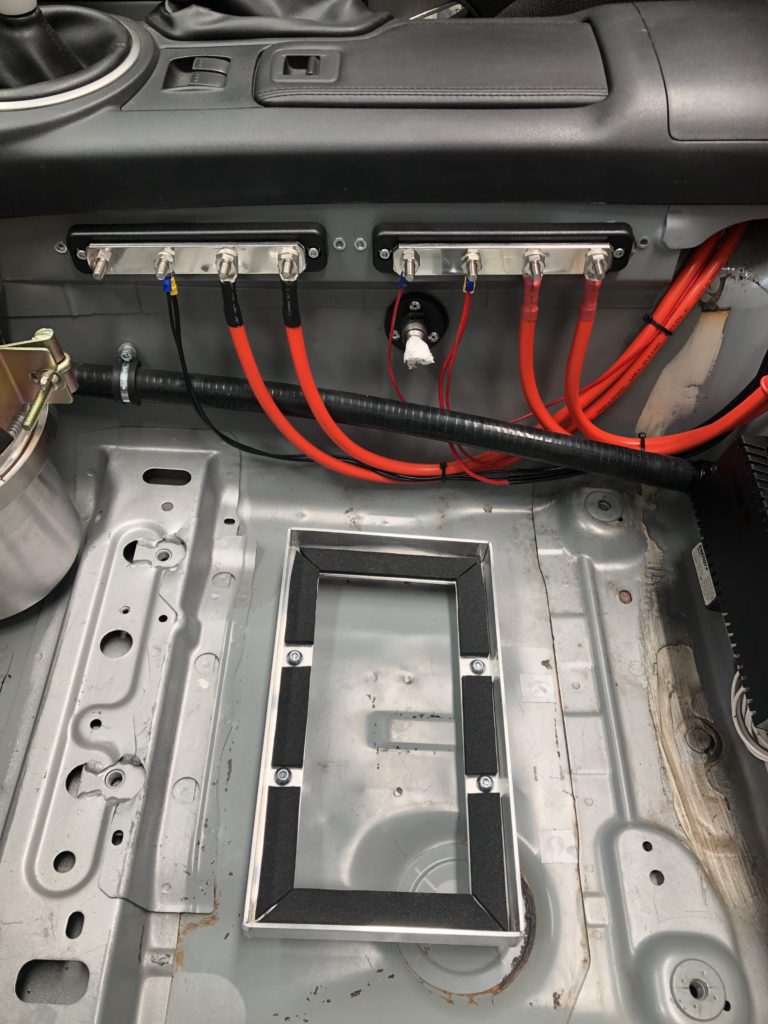
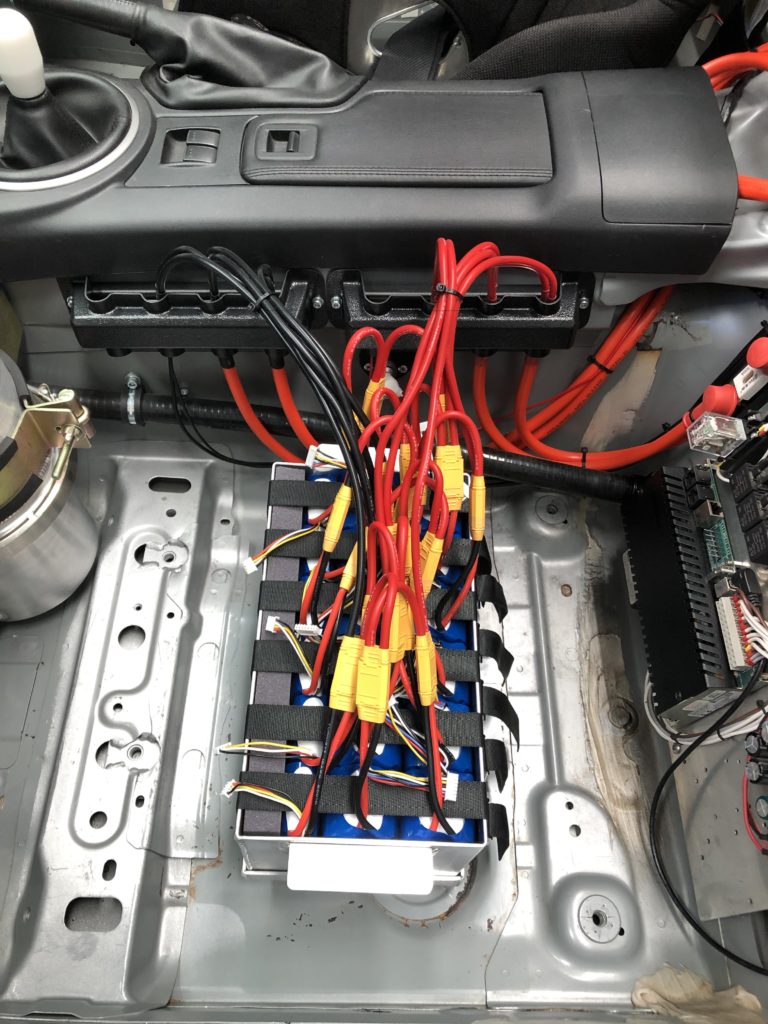
From the main DC bus to the ESCs, cable size has been increased to 35mm2 per ESC. For protection a new 500A fuse has been installed and the 500A DC contactor has been carried over.
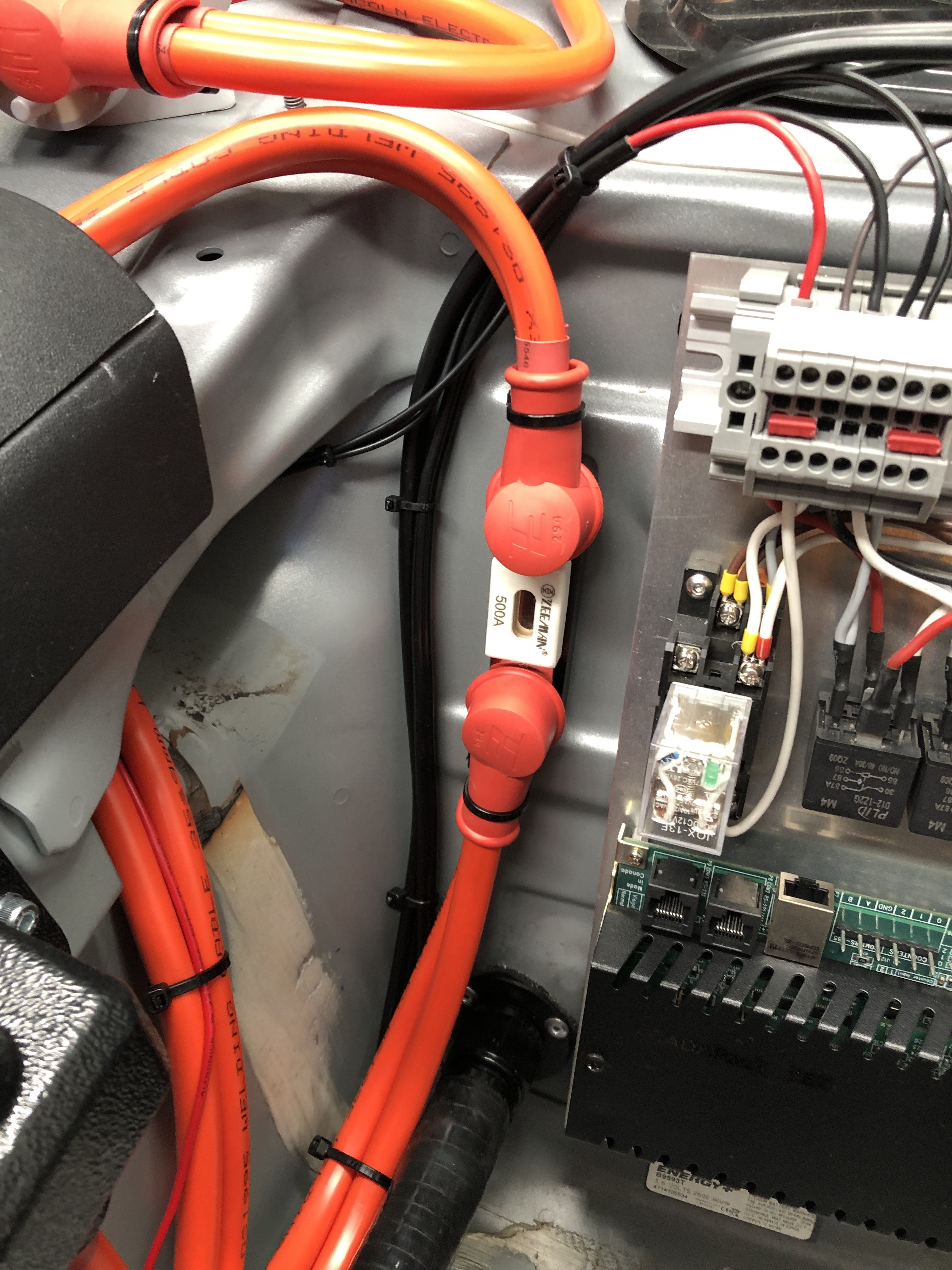
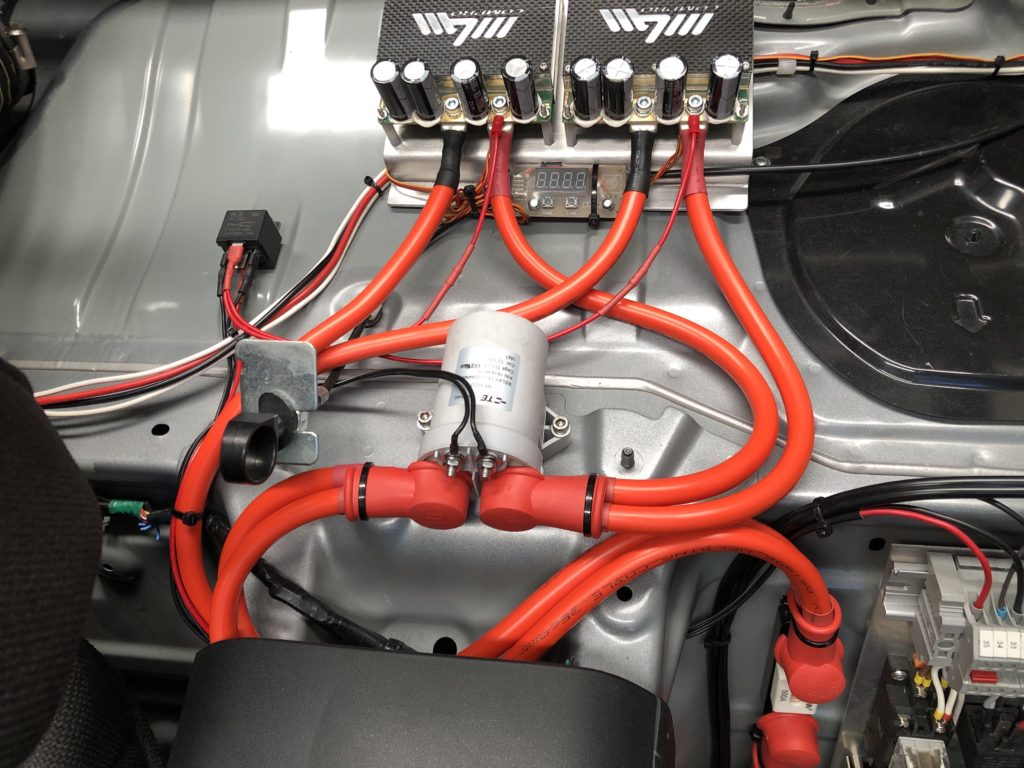
The ESCs have also been relocated to sit in between the battery and electric motors and are now mounted side by side.
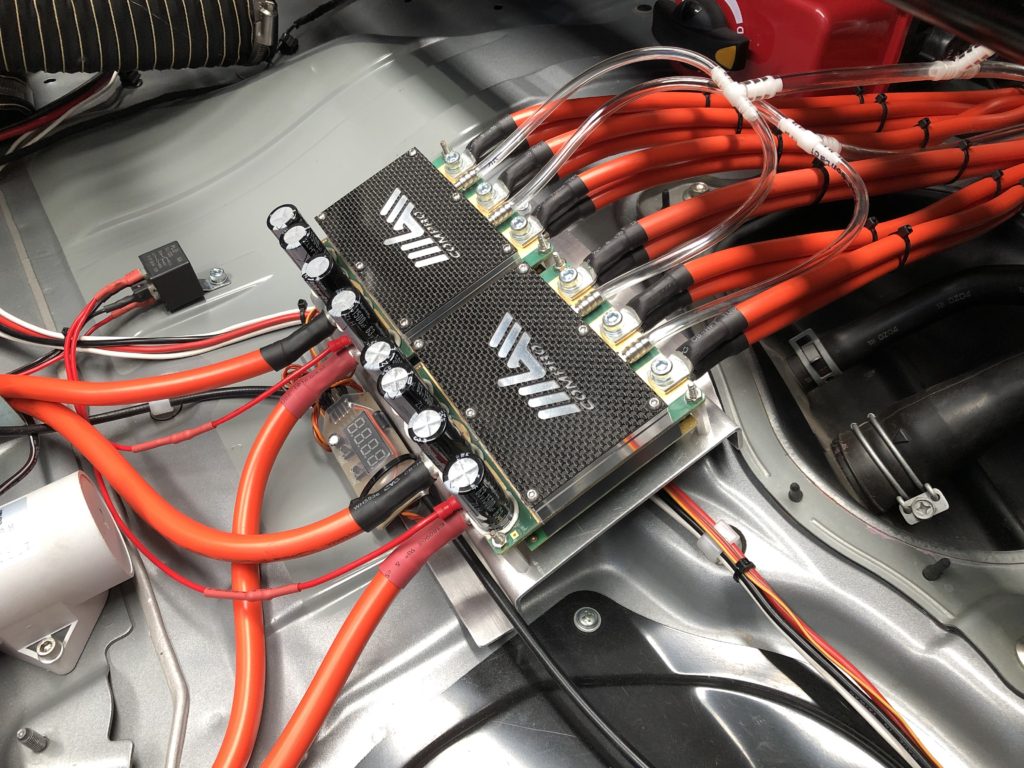
From ESCs to each motor phase, cable size has been increased to dual 16mm2 (total 32mm2) per phase.
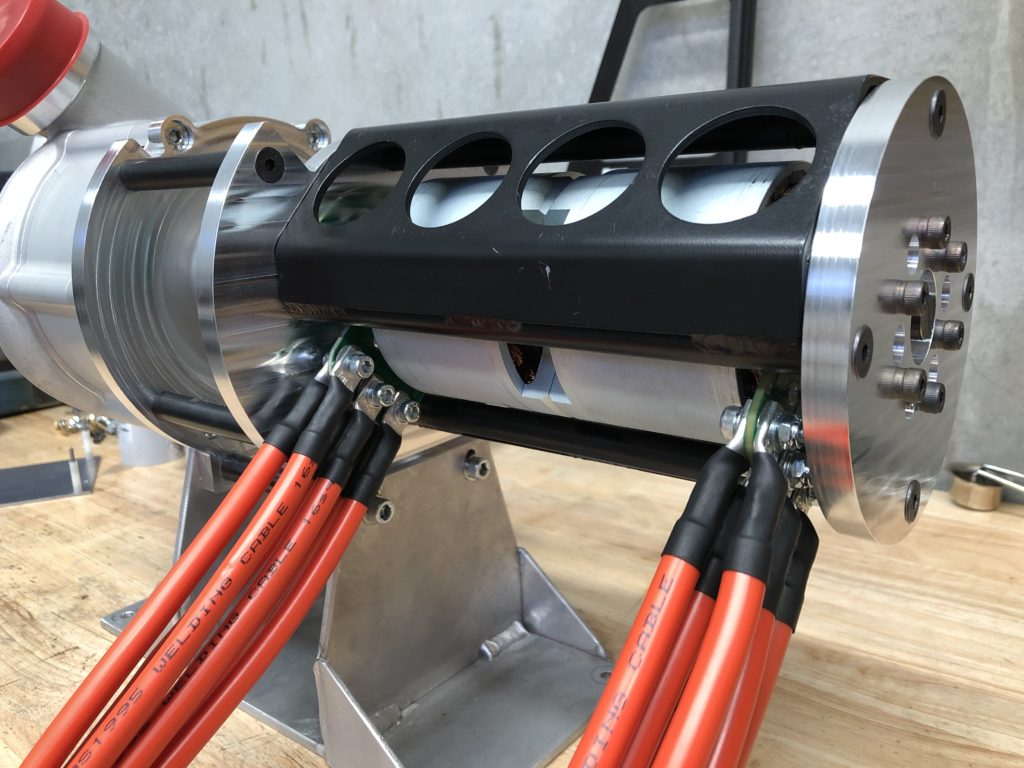
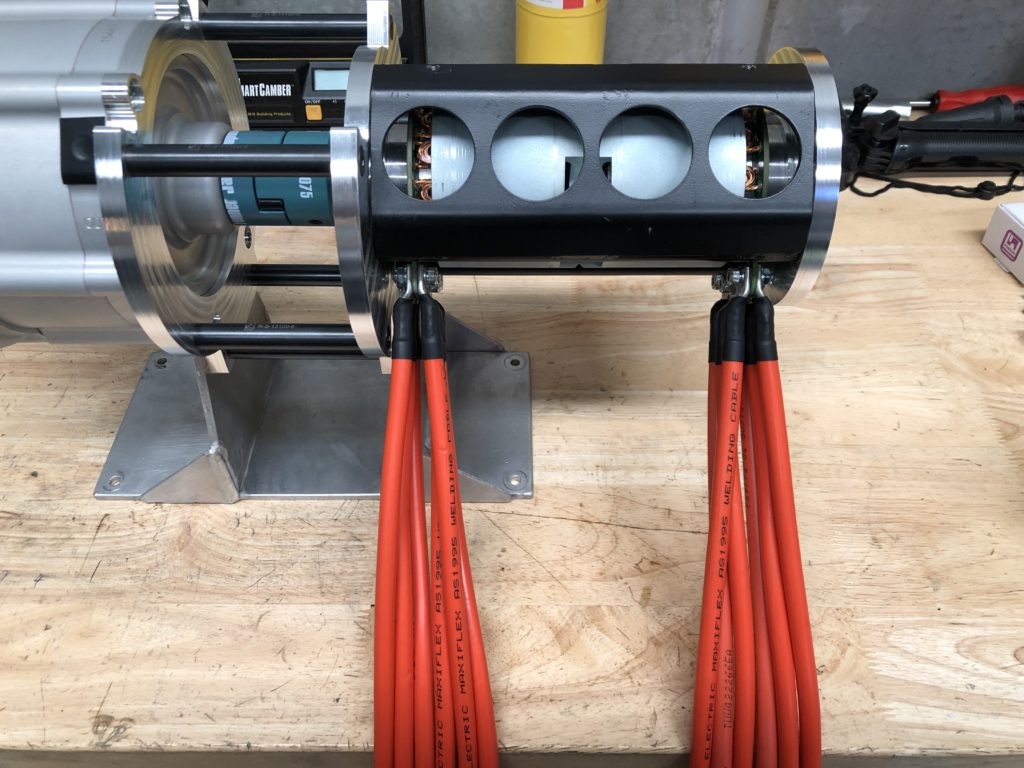
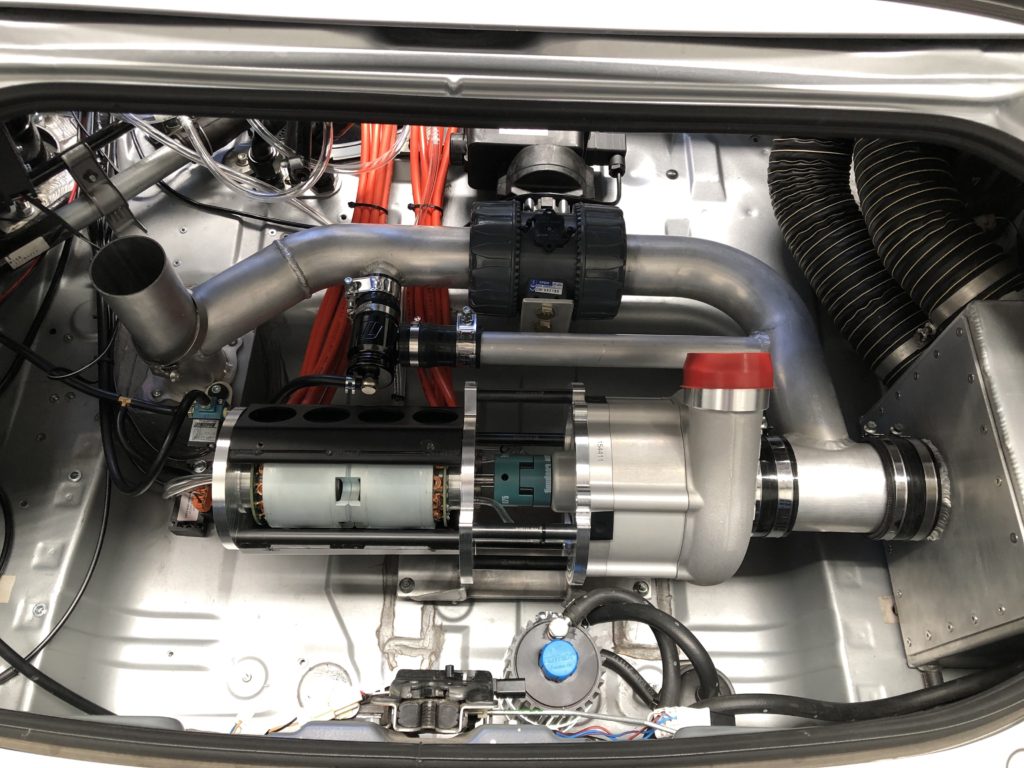
The inductance of the cables between the battery and electronic speed controllers has increased due to the increase in both cable length and cross sectional area. To deal with this, two 10,000 uF capacitor banks were assembled using low ESR electrolytic capacitors. These were wired to to the input terminals of the electronic speed controller.
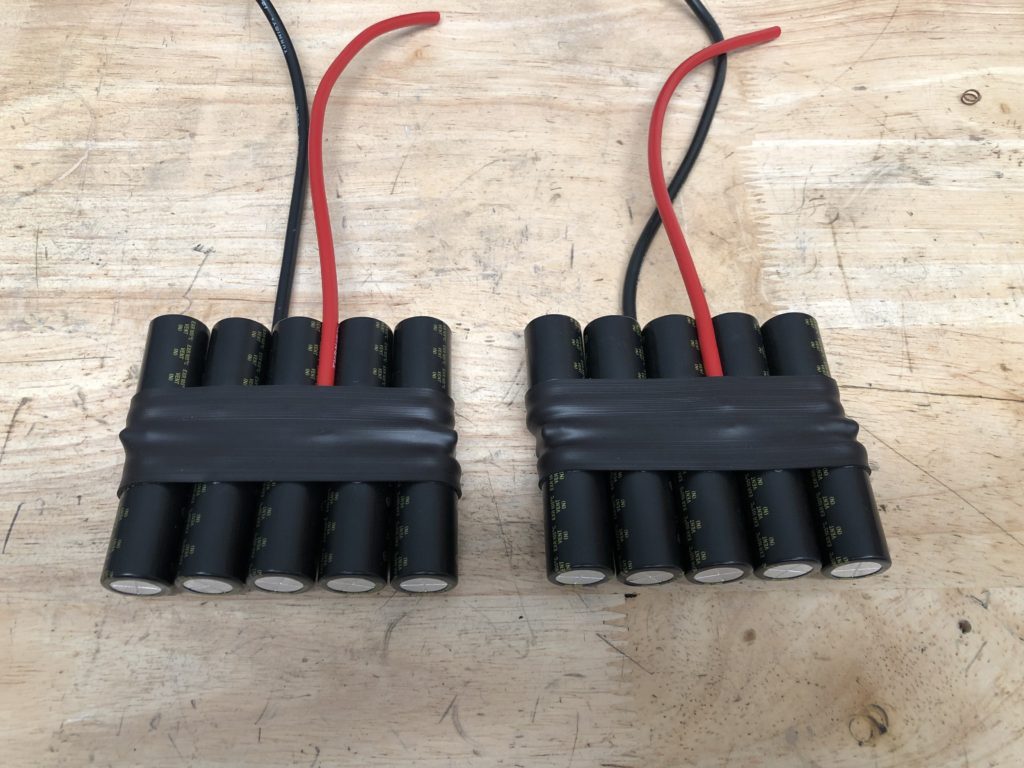
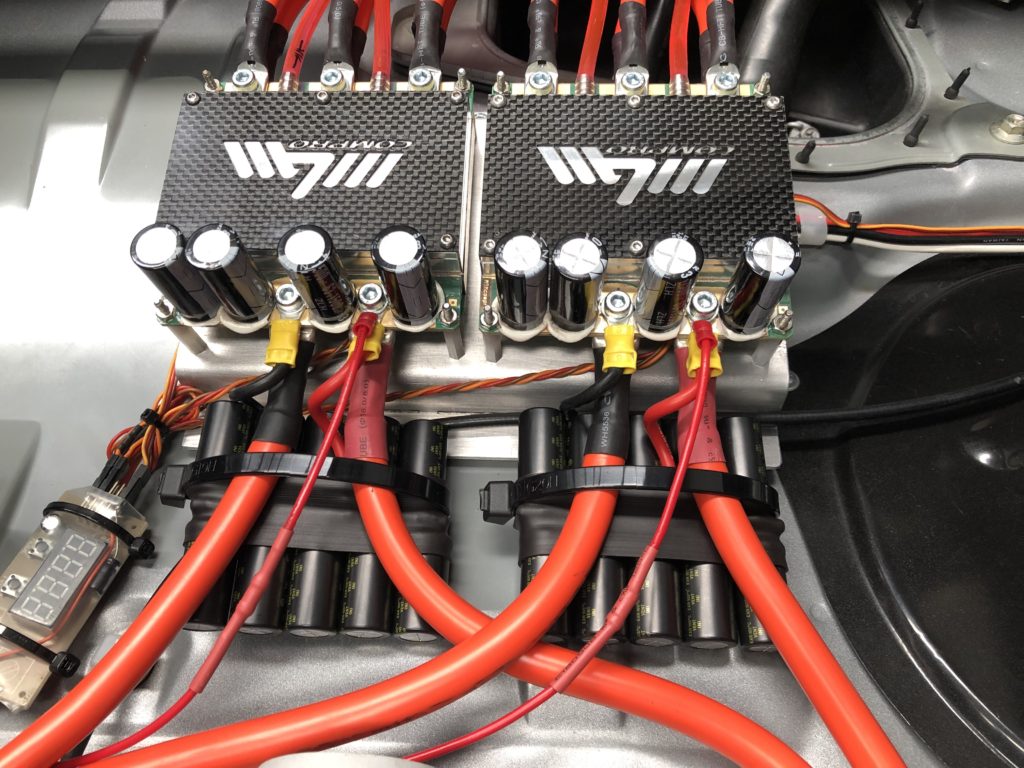